- Turbochargers are very reliable: less than 0.5% of turbos fail due to any fault within the turbo itself.
- Almost ALL turbo failures are because of problems with oil contamination, oil starvation, foreign object impact damage or oil leakage due to excessively restricted air intake/exhaust system.
Before installing a new turbo, always determine and correct the issue which caused the original turbo to fail, or the replacement turbo will almost certainly fail for the same reason.
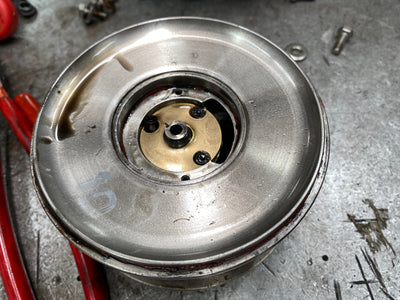
What causes turbocharger oil seals to leak?
A Turbocharger’s turbine and compressor wheels are operating at anywhere between 150,000 and 250,000 RPM, depending upon the specific turbo model.
In addition, the turbine end of the turbocharger can be operating at temperatures approaching 1000 degrees Celsius.
The turbo relies on a thin film of oil to provide the hydrostatic support of the main shaft and support bush (“bearing”) within the turbocharger. This oil is kept in place by seals at both the compressor and turbine ends of the bearing housing of the turbocharger.
These seals bear no resemblance to conventional oil seals. They are more closely related to miniature engine piston rings. They require positive air pressure within the compressor and turbine housings to prevent oil leakage into either housing. Any restriction to the turbo compressor inlet will result in sufficient vacuum within the compressor housing to permit oil leakage past the compressor end seal. If there is any restriction to the turbo oil drain, or the engine suffers from excessive crankcase pressure (I.E., as a result of a malfunctioning PCV system, or worn cylinder piston rings) the turbine end seal will usually leak into the turbine housing. Either scenario, compressor or turbine seal leakage, results in turbo lubrication oil loss.
What are the usual causes of leaking turbocharger oil seals?
Compressor wheel (“cold side”) leakage is typically caused by one or more of the following:
- Blocked or partially restricted (dirty) air filter element
- Restrictive aftermarket air filter element (Even when new)
- Restrictive aftermarket snorkel design
- Aged rubber ducting between air cleaner housing and compressor inlet to turbo, collapsing when warm
Turbine wheel (“hot side”) leakage is typically caused by one or more of the following:
- Oil drain hose partial collapse or damage
- Malfunctioning PCV (Crankcase Ventilation) system
- Engine cylinder leakage as a consequence of worn piston rings, or scored cylinder walls
- Physical damage to the turbo’s rotating parts, as a consequence of bearing failure caused by contaminated, or partially starved oil supply (See separate relevant fact sheets)
Recommended steps for the prevention of leaking turbocharger oil seals.
- Always use OEM air cleaner filters and change them at no longer than 5,000 KM intervals. (Shorter when used in the Outback). “Blowing Out” with compressed air is NOT an acceptable alternative to replacing of the air cleaner elements. When traveling in the Outback, at least two new, spare OEM air filter elements should be carried at all times.
- Ensure that the rubber hose connection between air cleaner housing and turbo compressor inlet has not degraded with age. (This test can only be carried out with a hot engine compartment).
- Only ever source aftermarket snorkels from companies who can provide air flow data on their product.
- Ensure the engine PCV system is operating in accordance with OEM specifications.
- Ensure engine cylinder compression and more importantly, cylinder LEAKDOWN are within OEM specifications. (The latter should never exceed 10%, in the worst case).
- Ensure any flexible hose in the oil drain is neither kinked nor internally degraded with age.
For more information go to www.cateran.com.au or call the Cateran Technical Hotline on 1300 176 071
Download a printable version of this article here